Music WireDomestic music wire development
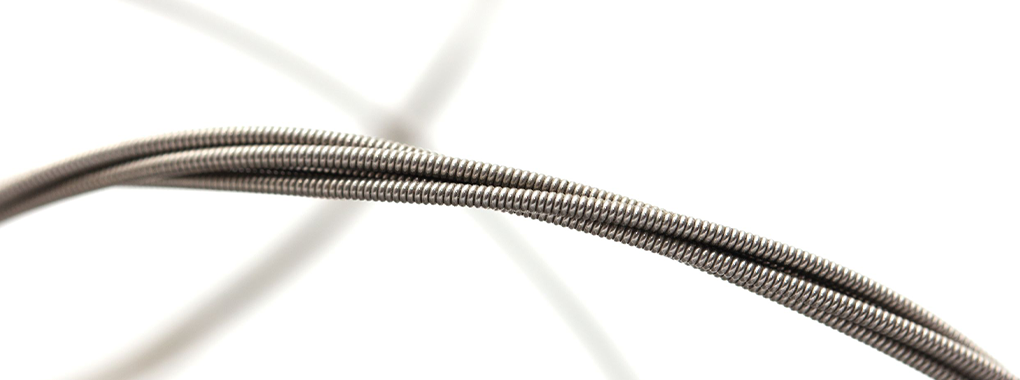
Domestic music wire development
Domestic manufacturing of music wire in Japan began in 1950, through the cooperation of Nippon Musical Instruments Manufacturing Co., Ltd. (today's Yamaha Corporation) and Suzuki Metal Industry Co., Ltd. (now Nippon Steel SG Wire Co., Ltd.).
Both Nippon Musical Instruments Manufacturing and Kawai Musical Instruments produced aircraft propellers during the war, but the factories burned down as a result of air strikes in the Hamamatsu area, which was a major setback. In addition, there was almost no demand for piano wire or other such goods immediately after the war. Suzuki Metal Industry, which produced the first domestic piano wire, was forced to reduce the number of their employees to 47 to survive the postwar recession. Nippon Musical Instruments Manufacturing, however, made an unusually rapid recovery for the industrial world at that time. The company restarted piano production in 1947 and completed its first full concert grand piano in 1950. Managing Director Genichi Kawakami, who was given much of the credit for restoring the company so quickly, was appointed President that same year.
Suzuki Metal Industry, though still struggling, was able to continue manufacturing piano wire. In 1949, they discovered through Aizawa Industry (now Itoshin Musical Co., Ltd.) of Hamamatsu, which handled piano wire for guitar strings, that a higher-grade piano wire called music wire had not yet been produced domestically. They also learned that Nippon Musical Instruments Manufacturing was looking to procure domestic music wire for their future instruments. Yutaro Murayama, President of Suzuki Metal Industry, immediately visited Nippon Musical Instruments Manufacturing and met with President Yoshikazu Kawakami, Executive Managing Director Aisa, Purchasing Division Manager Kubono and others to offer to develop this wire, for which he received their approval. This was how Japanese domestic music wire production began. However, Nippon Musical Instruments Manufacturing started their own research around this time as well, and provided useful information to Nippon Steel SG Wire. The first prototype was completed and delivered that year. It received a positive evaluation, and a larger order was placed for a No. 2 prototype, which began trial production. But this effort was not as successful, and a hard struggle ensued.
The fall of 1950 saw a huge uproar at Nippon Musical Instruments Manufacturing. The new CF model full concert grand piano that was announced in the summer was severely panned by critics. Among the stinging criticism..."At forte, it sounds like it could be a German piano that's been worn out for a couple of decades. That is, the precision of the string wires is so poor that they emit a hard, colorless sound. The bass tone is unfocused and slack, like a loose waist belt, and the treble sounds are dull. It is likely to be a long time before this instrument deserves our respect."
The expression "like a loose waist belt" may not be readily understood by those who do not wear Japanese garments, but the problem it pointed out was clear: the poor quality of the wire. At this time, the music wire, felt and cloth being used were all imported, so the domestic music wire then being developed was not the cause. In response to the criticism, Geniichi Kawakami, who had just become the company's president in September himself, wrote a rebuttal, restating his commitment to further improve their concert grand piano. The specificity of the flaw would seem to indicate that the war had affected German industrial production to the point that German music wire had not recovered to its pre-war standards either.
Yamaha continued to improve its full concert grand from that point on, with great success. Their current flagship model CFIIIS has been adopted as an official piano at music festivals around the world, and earns extremely high praise from judges and performers. The Japanese broadcaster NHK has aired a program, "Project X," about the circumstance that led to its development and success.
The launch of the piano was tough, but music wire development was difficult as well. Even after generating 30 tons of waste, they had not been able to produce a No. 2 prototype that met the standards they had specified. The production volume of piano wire at that time was only about 20 tons per month, so this was a serious problem. Yutaro Murayama encouraged the technical staff, who were ready to give up, and spurred them keep trying, saying "Success with this wire will lead to success at all levels of Suzuki wires, so you simply cannot stop halfway." The staff returned to the task, making hundreds of prototypes while altering materials, heat treatment and wire drawing processes. Their dedicated effort eventually paid off, and they finally succeeded in developing a music wire that met the demands of Nippon Musical Instruments Manufacturing.
Despite the company's success in overcoming obstacles to create fine music wire, financial conditions at Suzuki Metal Industry were grim at that time, to the point where they struggled to meet payroll, and didn't always succeed. Swedish wire was the best material for the music wire, but there was no contract money to pay for imports. Murayama decided to visit Nippon Musical Instruments Manufacturing and ask for a one million yen advance to be used to buy foreign wire. Of course, the initial answer was "no," but his sincerity and passion made an impression, and in the end, he was able to obtain the funds. A million yen in those days was a considerable amount of money. Mr. Murayama often said, "I can not forget the happiness caused by President Kawakami's generosity at that time.
Mass production of domestic music wire began in 1952. The yield was initially 50%, but by 1954 that had increased to 95?98%. The company continued to use Swedish wire materials but from around 1966 they began to evaluate materials from Yawata Steel Works (now Nippon Steel Corporation), with the aim of making an all-domestic product. After thorough testing, they succeeded in doing so in 1979.
Then as now, Japanese people have a weakness for the implied superiority of foreign-made goods. Even after achieving domestic music wire production, there was a little voice that said, "foreign products are preferable." So, using two identical pianos, the company conducted blind tests between imported and domestic products, to demonstrate that there was no difference. One of the pianos they used remained until the year 2000, but was regrettably disposed of that year when the bachelor dormitory was dismantled.
In subsequent research, it was discovered that Sumitomo Electric Industries Ltd., which had been involved in making the wartime aircraft propellers, tried to commercialize domestic production of music wire in 1948, ahead of others. However, there were a high percentage of defects in the flat striking test, which compresses the wire diameter by up to half, and in 1950 sourcing was switched to the Suzuki Metal Industry product, for reasons noted above.
(Reference: One Hundred Year History of Sumitomo Electric Industries, edited by Sumitomo Electric 100th anniversary editorial committee in 1999)