Music WireHistory of wound strings
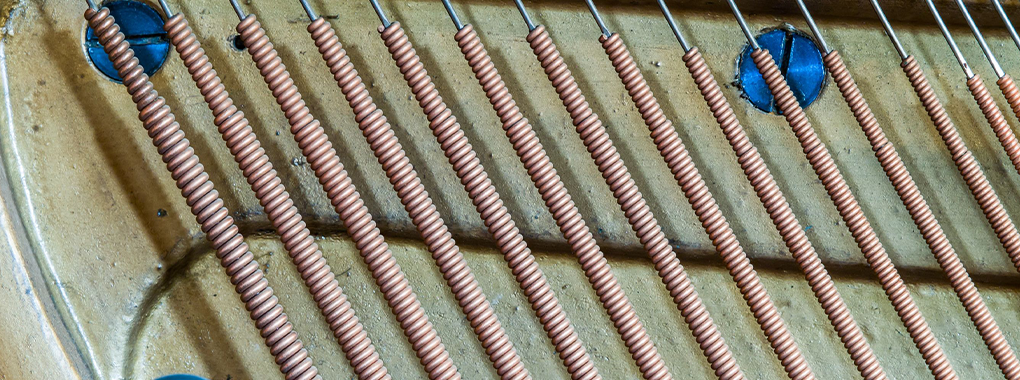
History of unison strings
Strings in the bass section, on the other hand, use windings to increase their mass?another time-honored technique that dates back to at least the 16th century. Creating lower tones in a stringed instrument requires longer or thicker strings. The strings of the highest "C" note in a modern piano are about 5 cm long. Lowering the pitch by an octave doubles the length required, so a note one octave below needs 10 cm strings. This relationship is the same for other stringed instruments as well. As the lowest "C" note on a piano is seven octaves lower than the highest, using the same wire would require strings over 6 m long. In order to keep the instrument a reasonable size, we use thicker strings for the lower notes instead.
Late 18th century square piano, using wound strings
Manufactured by F. Beck around 1785
Photo provided by Hamamatsu Museum of Musical Instruments
Violins and guitars, which have an even longer history than pianos, originally used gut strings made from sheep intestines. Since there is a limit to how thick a single gut string can be, a technique developed of twisting several pieces of gut together before drying, then polishing to form a smooth, thicker string. These rope-like gut strings were used for both plucked and bowed string instruments.
Gut strings overwound with thin metal wire first appeared in Italy in the year 1660, where they were initially used for violins. There are two main types of winding: open or half winding, which leaves a space between the loops of wire, and closed winding, where the wire is wound tightly against itself. These two methods are used according to the sound range desired. Open winding is applied to the higher registers, while closed winding is used for lower tones, as the tighter winding creates a denser, heavier string.
When was the winding technique first applied to piano strings? In the literature, Sebastian Erard of France visited John Broadwood & Sons in England in 1808 and 1815, where he studied current techniques and then returned to Paris to develop techniques of his own. It seems that he may have been first to change the bass strings from brass wire to steel wire wrapped with brass wire. When looking at the strings of pianos and harpsichords in the Hamamatsu Museum of Musical Instruments, we find both open- and closed-wound bass strings in several square pianos dating from around 1785 to 1805. So we can consider wound piano strings to be a late 18th century innovation. This technique was not applied to grand pianos until somewhat later, around 1820. The reason for this was that the grands did not have the same size limitations as the more compact square pianos, which needed to increase the mass of the strings, instead of their length. The smaller instruments also had less robust frames, which made it impossible to adopt thicker strings. This gave them less sustained resonance and a more attenuated sound. The winding technique was intended to address these characteristics as well.
- Since the instruments collected in the Hamamatsu Museum of Musical Instruments represent a dynamic evolution, it is possible that expendable parts such as strings and hammers may have been changed from the original, prior to being added to the collection.
Winding factory in the old days
The structure of the manual winding machine appears unchanged to this day.
Reference: Five Lectures on the Acoustics of the Piano
Although the shape of the winding wire is normally round, Hamilton devised a flat-wound string in 1874. This had little bearing on pianos, but was beneficial for violins, as it increases the contact area with the bow. Strings with a core of gut or nylon wrapped in flat gold, silver or aluminum wire are still in use today. Bass (double or contrabass) strings?which we would expect to be overwound, as they mainly produce sounds in the lower registers?utilize not only double- but even triple-wound strings, and electric basses often use flat-wound strings. For the bass strings of the harp, fiber is wound around the metal core wire, then overwound with flat copper wire or nylon. As you can see, the types and configuration of windings vary according to the musical instruments involved.
Structure of a violin string: Tonica G string by Pirastro
At first sight, this violin string looks like a common metal wire. If you were to disassemble it, though, you'd find that it is more complex. A core bundle of synthetic strands is wound with a round wire of Fe-Ni alloy and then overwound with a final layer of flat silver wire.
Structure of a guitar string: G string by Martin & Co.
Round brass wire is wound around a core of hexagonal cross section piano wire.
Piano string: Appearance of the thickest double winding
The thicker part on the right is double-wound.
The middle part shows single winding, while the black part on the left is the core wire.
Piano string: At the base of the winding
The core wire is flattened at both ends, which makes the winding less susceptible to loosening.
Piano string: Structure of double winding
As you unwind this thick copper wire, a thinner winding appears within. The windings are thicker than that used for guitar strings, and the direction of winding is reversed between the inner and outer winding.
The biggest potential problem with windings is the tendency for them to loosen from the core during use. Especially for pianos and bowed or plucked string instruments played at high amplitude, this can easily happen. Kali and Happel in 1885 devised a triangular or polygonal core wire as a solution to this problem. Their technique is still in use today, with hexagonal core wires in guitar strings, but piano strings employ a slightly different method. First is to flatten both ends of the core wire around which the copper wire will be wrapped. This is called "flat striking." Next, the copper wire is attached and wrapped around the core, including the flattened part. Even a soft metal such as copper has slight elasticity, so it tries to return a little to its prior state after winding. This is called "spring back." However, due to the flat section of the core wire, the winding cannot rotate, thus preventing it from loosening.
Advanced technology and technique are necessary to maintain consistent quality, since winding angle, speed, wire tension and other factors in the winding process all affect the tonal character of the strings. Today, advances in machining have made it possible to produce considerably higher-performance windings. Still, even the best machinery is no substitute for skilled and experienced workers, and dedicated artisans carefully handcraft each concert grand piano.